In the realm of thermal management, spiral heat exchangers stand out as an exemplary solution for efficient heat transfer. Their innovative design, which features spiraled channels for fluid flow, maximizes heat exchange while minimizing space requirements. Unlike traditional heat exchangers, spiral units are highly effective in handling fluids that may cause fouling, making them a preferred choice in various industrial applications. Whether in chemical processing, food and beverage production, or energy generation, the spiral heat exchanger is a remarkable advancement in engineering.
What is a Spiral Heat Exchanger?
A spiral heat exchanger is a type of heat exchanger that consists of two concentric spiral flow channels, allowing two different fluids to transfer heat between them. One channel handles the hot fluid, while the other is designed for the cold fluid. These fluids flow in a counter-current manner: one fluid enters at the center of the unit and moves toward the outer edge, while the other fluid enters at the periphery and flows toward the center.
Design Features
The structure typically includes a flange inlet on the front face with the outlet located on the top. The second fluid’s inlet is also positioned on the top, while its outlet is located on the rear face. Inside the heat exchanger, two sheets of metal spiral together around the interior, forming separate channels for the two fluids. This channel design ensures that the two fluids remain completely separated during their flow through the heat exchanger.
How It Works
The operation of a spiral heat exchanger is based on the principles of heat transfer and fluid dynamics. Here’s a breakdown of its working mechanism:
Single and Long Curving Flow Passages
Spiral heat exchangers feature single and long curving flow passages with a uniform rectangular cross-section. This design ensures superior flow distribution, intense turbulence, and high heat transfer coefficients—typically 50-100% greater than those found in shell-and-tube heat exchangers. The effective flow distribution enhances the overall thermal performance of the unit.
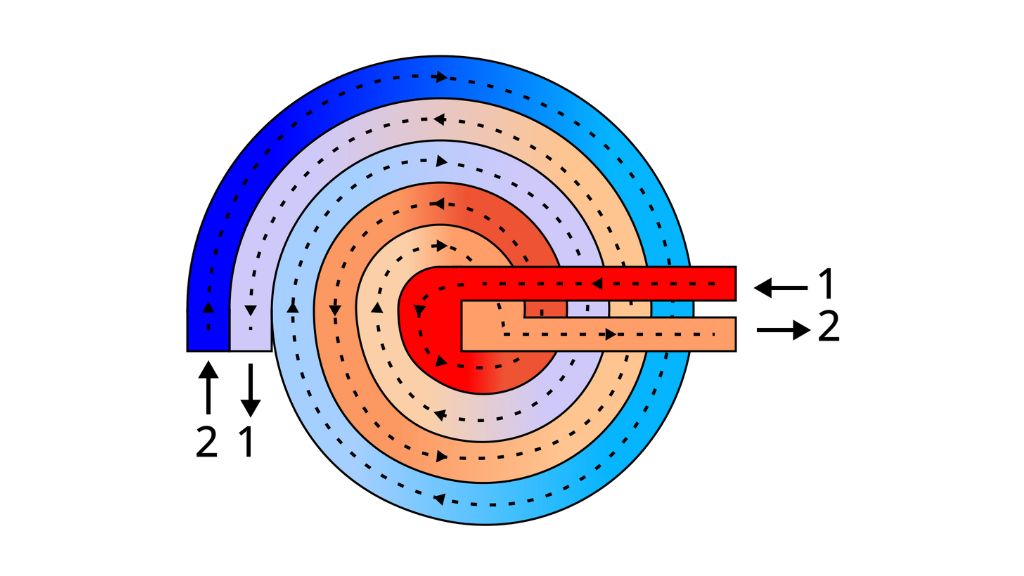
Countercurrent and Co-current Flow
Spiral heat exchangers predominantly operate in a true counter-current flow configuration, which allows for close temperature approaches and temperature crosses. However, a co-current flow design can be advantageous in specific scenarios, particularly when handling fluids that are prone to gelation, burning, freezing, or similar issues related to skin temperature fouling.
Self-Cleaning Mechanism
One of the notable advantages of spiral heat exchangers is their ability to minimize fouling. The spiral’s single-flow passages induce high shear rates that effectively scrub away deposits as they form. This self-cleaning effect reduces fouling and makes spiral heat exchangers ideal for handling tough fluids such as process slurries, sludge, and media containing suspended solids or fibers.
Flow Process
The first fluid enters the heat exchanger, filling the chamber, and flows around the channel to the outlet. Simultaneously, the second fluid enters via the top, flowing around the channel and into the chamber, where it then exits. The two fluids enter and exit at different temperatures, allowing efficient heat transfer.
Advantages of Spiral Heat Exchangers
Spiral heat exchangers offer numerous benefits that make them a favorable choice for various applications:
- High Efficiency: The combination of counter-current flow and turbulent mixing leads to superior heat transfer efficiency, reducing energy consumption.
- Compact Design: The spiral configuration allows for a compact footprint, making these heat exchangers suitable for installations with limited space.
- Reduced Risk of Fouling: The unique self-cleaning design minimizes fouling, ensuring longevity and consistent performance.
- Versatility: Spiral heat exchangers can handle a wide range of fluids, including viscous liquids and slurries, making them adaptable to various industries. They are particularly effective in installations where sludge-like substances are processed, such as in anaerobic digesters.
- Easy Maintenance: The compact design requires minimal space for installation and servicing. Removable covers provide easy access to interior heat transfer surfaces for field inspections, routine maintenance, or manual cleaning when necessary.
- Cost-Effective: With lower maintenance needs and high efficiency, spiral heat exchangers can lead to cost savings over their lifespan.
Disadvantages of Spiral Heat Exchangers
Despite their many advantages, spiral heat exchangers also have some drawbacks:
- Initial Cost: The initial purchase price of spiral heat exchangers can be higher than that of traditional shell-and-tube designs, which may deter some users.
- Limited Pressure Drop: Due to their design, spiral heat exchangers may have a limited ability to handle high-pressure applications compared to other types.
- Maintenance Complexity: While they are generally low-maintenance, any fouling that does occur may require disassembly for thorough cleaning, which can be more complex than for other designs.
Maintaining and Servicing Your Spiral Heat Exchanger
Regular maintenance is essential to ensure optimal performance and longevity of your spiral heat exchanger. Here are some key maintenance practices:
Regular Inspections
Conduct periodic inspections to check for signs of fouling, leaks, or wear and tear. Look for changes in temperature differentials and flow rates, which may indicate issues with heat transfer efficiency.
Cleaning Protocols
Implement a cleaning schedule based on the nature of the fluids being processed. For fluids prone to fouling, more frequent cleaning may be necessary. Use appropriate cleaning agents that are compatible with the heat exchanger’s materials.
Monitor Performance
Regularly monitor the performance of your heat exchanger, including temperature, pressure, and flow rates. Anomalies in these parameters can signal potential problems that require immediate attention.
Professional Servicing
Consider engaging professionals for servicing, especially for disassembly and thorough cleaning. They can also conduct comprehensive assessments to ensure that all components are functioning optimally.
For industries looking to enhance their thermal management systems, understanding the workings and benefits of spiral heat exchangers is essential. With proper maintenance and servicing, these devices can deliver outstanding performance and reliability for years to come.